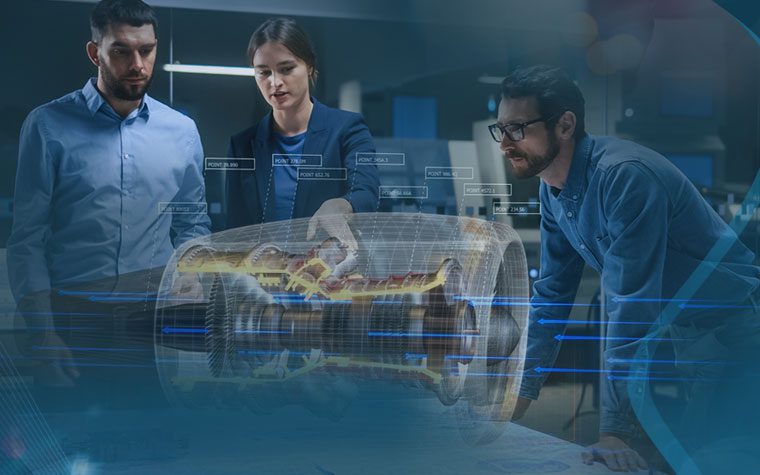
How Finite Element Analysis (FEA) is changing the landscape of Aircraft Structural Design?
An aircraft structure is a highly complex assembly consisting of numerous components, subcomponents as well as sub-subcomponents. This complexity makes it extremely crucial to ensure that the design is highly safe and secure for its purpose. There is a need to be able to ascertain the durability of the structure, i.e., whether the aerospace device will wear out, break down or perform the way it was conceived in the face of different stressors. Even a minor detail, such as a riveted joint, would require validation using structural analysis. And that is where Finite Element Analysis (FEA) comes into the picture.
Because of the complexity, several structural elements involved, and the way different components/assemblies are connected, analytical structural analysis methods [1,2,3] pose enormous challenges in stress calculations. It requires a lot of assumptions to simplify the equations resulting in a structure that is heavy, thereby reducing the fuel efficiency and subsequently increasing the cost of aircraft operation.
Finite Element Analysis (FEA) has emerged as a savior in aiding analytical structural analysis in terms of getting the inputs required for analytical methods, not only with quick turnaround time but with superior accuracy too. Engineers create a mesh that splits the area into a discrete number of elements for which the solution can be calculated and subsequently interpolated across the whole area.
Since aircraft design undergoes multiple iterations during its design cycle and repetitive calculations with quick turnaround time are an essential part of a good design, FEA is truly a boon for aerospace engineers.
Different Types of FEA for Aircraft Structure Validation
Various types of analyses are required for validation of the entire aircraft structure to comply with FAA/EASA regulations [4,5], and hence Finite Element Analysis is useful.
Some of the analyses that can be carried out are:
- Static Strength Analysis, wherein every item is checked for its adequate strength/margins at the limit and ultimate loads as defined by the regulations [4,7,8].
- Stiffness Analysis is required for clearing the structures under dynamic loads and has adequate margins under these loads. This involves getting the frequency response of the structure and checking that dynamic forces are within limits [5,7,8].
- Advanced Dynamic Analysis, such as:
- Aeroelasticity to study the coupling of aerodynamic forces and elasticity of the structure and its impact on the structure [5,7,8].
- Impact/Crash Analysis to validate the structures against crash, bird impact, etc., involving high strain rate response of the structures [6,7,8].
- Aircraft Seat Test Correlation Studies under dynamic loads prescribed in regulations [6,7,8].
- Design and validation of structures for static and dynamic tests [7,8].
- Static Strength Test Correlation by simulating the test conditions [7,8].
- Static Strength Validation of Tooling Jigs and Fixtures.
- Correlation of Ground Vibration Tests for modal frequencies and mode shapes.
- Correlation of Coupon Tests for material characterization [7,8].
- Many other analyses are required during the design of aircraft and its operations.
The basic FE Analysis process is given below.
There is multiple pre- and post-processing software available for the creation of FE models and processing of the results respectively. These can be customized to enhance the turnaround time by writing API (Application Programming Interface) scripts. The results of the Finite Element Analysis can then be used for hand calculations and one can arrive at Margins of Safety.
Things to Consider While Creating an FE Mesh
- Cost of analysis shall be minimized by choosing mesh density judiciously, based on the structural details and the regions of interest in the component.
For example, in the case of dynamic analysis, a coarser mesh is sufficient if the mass and stiffness are captured accurately. A feature such as a lightening hole in the wing rib shall be meshed with finer element sizes to capture the stress concentration effects.
- For implicit analysis, the accurate definition of contacts between two components is important to capture the dynamic load transfer. Also of importance, is defining precise high-strain rate data for capturing dynamic stresses.
- For aeroelastic analysis, the mass distribution should be captured accurately to get proper modal frequencies and mode shapes which essentially are used for calculating flutter and buffeting speeds.
- It is equally important to possess a thorough knowledge of the certification/regulatory requirements before carrying out the Finite Element Analysis.
Finite Element Analysis, in general, and with the latest advancements in software and hardware, has resulted in carrying out structural analyses more accurately with a reduction in the design cycle.
More importantly, certification authorities are accepting Finite Element Analysis as a part of the design cycle. It is being used extensively in all sub-domains of aircraft design starting from aerodynamics design to flight-testing activities. It is prudent for any aircraft design organization to build a team and use this process effectively to reduce the cost of product development.