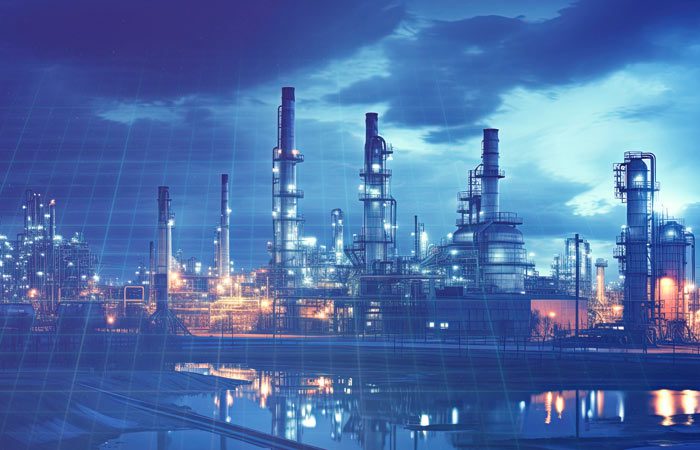
7 Key Trends in Static and Rotating Equipment Engineering
Both stationary and moving machinery engineering are an important field in many industries, including manufacturing, electricity generation, chemical processing, and oil and gas. The term “static equipment” describes the equipment that is permanently installed, including pressure vessels and storage tanks, piping systems and related hardware (such as valves and fittings), relief devices, vent hardware, and emergency shutdown/control systems. Pumps, blowers, fans, and compressors, on the other hand, can be employed to transport hazardous materials inside these systems. They are referred to as rotating equipment. The design, operation, and maintenance of static and rotating equipment are being shaped by a number of trends that are emerging as technology develops.
Here are 7 key trends in static and rotating equipment engineering:
- Condition Monitoring and Predictive Maintenance
Sensors are used in condition-based monitoring, a sort of maintenance, to keep an eye on the equipment’s health. Before the equipment breaks down, this information can be used to arrange maintenance. Predictive maintenance, on the other hand, is a sort of maintenance that uses data and analytics to foretell when equipment would likely break. When maintenance is planned in advance of equipment failure using this knowledge, downtime and repair costs can be significantly decreased.
With the advent of advanced sensors and monitoring systems, there is a growing focus on condition monitoring and predictive maintenance of static and rotating equipment. By continuously monitoring equipment parameters, such as vibration, temperature, and pressure, maintenance teams can detect anomalies and potential failures before they occur, thereby minimizing downtime and maximizing equipment reliability.
- Digitalization and Internet of Things (IoT)
The integration of digital technologies and IoT is revolutionizing the static and rotating equipment industry. By connecting equipment to a network, engineers can collect, analyze, and interpret vast amounts of data in real-time. This data-driven approach enables better decision-making, improved equipment performance, increased productivity, and reduced operational costs.
- Advanced Materials and Coatings
There is a growing demand for advanced materials and coatings in static and rotating equipment engineering. These materials offer improved resistance to corrosion, erosion, and wear, thereby extending the lifespan of the equipment. Additionally, the use of advanced materials, such as composites, allows for lighter and more efficient equipment designs.
- Energy Efficiency and Sustainability
The focus on energy efficiency and sustainable practices is driving the development of static and rotating equipment that minimizes energy consumption and emissions. This includes the use of efficient pumps, compressors, turbines, and other equipment, as well as the adoption of renewable energy sources and energy recovery systems.
- 3D Printing and Additive Manufacturing
The advancements in 3D printing and additive manufacturing are revolutionizing the design and production of static and rotating equipment components. This technology offers increased design flexibility, reduced lead times, and cost-effective manufacturing of complex geometries. It also allows for on-demand spare part production, eliminating the need for large inventories.
- Remote Monitoring and Control
The ability to remotely monitor and control static and rotating equipment is becoming increasingly important. Through the use of remote monitoring systems and automation, engineers can monitor equipment performance, troubleshoot issues, and make adjustments from a centralized location. This improves operational efficiency, reduces the need for on-site personnel, and enhances safety.
- Increased Focus on Safety
Safety remains a top priority in static and rotating equipment engineering. There is a growing emphasis on designing equipment with enhanced safety features, such as fail-safe mechanisms, protective barriers, and advanced alarm systems.
The market for static and rotating equipment is constrained by both the possibility for equipment failure and the requirement for professional labor for installation and maintenance. The requirement for routine maintenance and the potential for equipment downtime are two difficulties facing the market for static and rotating equipment. Consequently, there is a growing emphasis on operator training, safety procedures, and adherence to industry norms and laws. Improvements in performance, dependability, efficiency, and sustainability are driving forces behind these advances in static and rotating equipment engineering. We can anticipate more developments in this area as technology advances, leading to equipment designs that are safer, more effective, and more ecologically friendly.