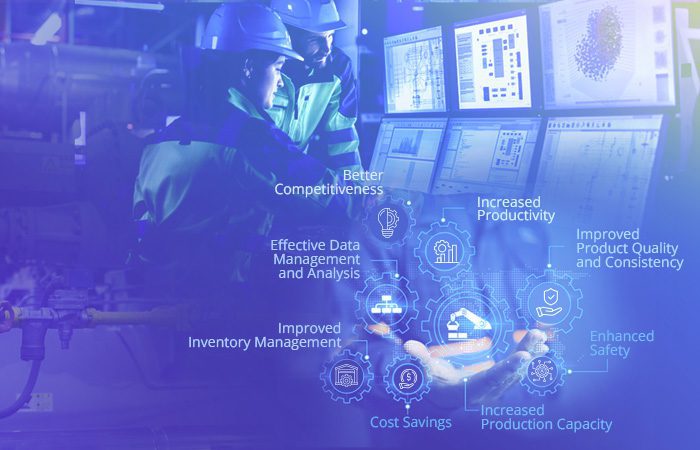
Decoding the Benefits of Plant Automation
Plant automation plays a vital role in modern industrial processes, and this trend is expected to grow aggressively in the future as well. It encompasses the use of advanced technologies and control systems to operate and monitor various aspects of plant operations and offers a range of benefits that can significantly enhance efficiency and productivity in various industries. Some of the commonly used automation technologies include the Industrial Internet of Things (IIoT), Artificial Intelligence, Robotics, Big Data, Cybersecurity, Additive Manufacturing, Immersion, and Visualization, to name a few.
Some of the visible benefits of plant automation include.
- Increased Productivity
Automation eliminates the need for manual labor in repetitive and tedious tasks, allowing machines to perform these tasks more efficiently and accurately. This results in higher productivity rates, as machines can work faster and for longer durations without the need for breaks. Automation helps optimize the use of resources such as time, materials, and energy. By eliminating wasteful practices and maximizing efficiency, businesses can achieve higher levels of productivity with the same or fewer resources.
- Improved Product Quality and Consistency
Automation ensures that processes are carried out with precision and consistency, reducing the chances of human error. This leads to improved product quality, as machines can consistently produce products to the same standard every time.
- Enhanced Safety
Automating dangerous and hazardous tasks can significantly enhance worker safety. By replacing humans with machines in tasks such as handling toxic chemicals or heavy machinery, the risk of accidents and injuries can be minimized. A well-designed automation strategy, coupled with proper training and oversight, can significantly improve safety in various industries.
- Cost Savings
While the initial investment in plant automation may be high, it can lead to significant cost savings in the long run. By increasing efficiency, reducing material waste, predictive maintenance, optimizing inventory levels, and minimizing human errors, automation can help streamline processes and reduce production costs.
- Increased Production Capacity
Automation allows for increased production capacity without the need to expand physical space or hire additional labor. Machines can operate 24/7 and can be easily programmed to adjust production levels according to the demand of the customers, without excess inventory. Robotics and other automation technologies can augment the workforce, allowing plants and manufacturers to scale production capacity without a proportional increase in labor costs, thereby providing manufacturers with the ability to scale their operations effectively.
- Improved Inventory Management
Automation systems can integrate with inventory management systems to ensure real-time tracking and optimization of resources. Automated inventory systems can optimize the storage and distribution of products, reducing handling costs, minimizing the risk of stockouts or overstocking, and improving overall efficiency. Integrating inventory management systems with suppliers’ systems can automate the ordering process, enhancing supply chain management and reducing lead times.
- Effective Data Management and Analysis
Automation can streamline data collection processes, eliminating the need for manual data entry and reducing the risk of human errors in data recording. Automated data analysis tools can process large datasets quickly, providing real-time insights. AI-powered algorithms can identify patterns, trends, and anomalies in data. By analyzing this data, plant managers can identify potential issues and bottlenecks, improve decision-making processes to streamline, and optimize operations, productivity, and efficiency.
- Better Competitiveness
With automation, businesses can improve their competitiveness in the market by producing high-quality products at a faster rate and at lower costs. This allows them to meet customer demands more effectively and maintain a competitive edge in the industry.
Essentially, plant automation can be of multiple types, namely partially manual processes, automated single machines, automated production lines, and end-to-end automated plants. Regardless, the future of plant automation for industries holds tremendous potential to revolutionize operations and drive efficiency. By embracing technologies like robotics, IoT, AI, and digital twins, industries can unlock new levels of productivity, quality, and sustainability. However, it is essential to address cybersecurity concerns and ensure a smooth transition to automated systems while providing necessary training to the workforce for skill adaptation.