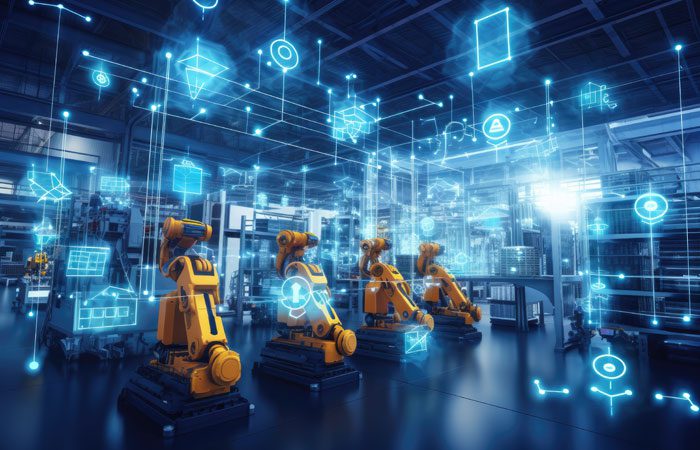
8 Leading Trends in IIoT for Manufacturing
The Industrial Internet of Things (IIoT) has been a transformative force in the manufacturing sector, reshaping processes, enhancing efficiency, and paving the way for a new era of industrial operations. According to a survey, 55% of respondents reported an reduced costs and 51% reported improved operational equipment uptime and availability owing to IIoT.
As we delve into the current trends shaping IIoT for manufacturing, it’s evident that the landscape is evolving rapidly, driven by technological advancements and the need for increased agility and competitiveness in the global market.
Here are the top 8 IIoT trends you must know about.
- Edge Computing Integration
One of the prominent trends in IIoT for manufacturing is the integration of edge computing. Edge computing involves processing data closer to the source, reducing latency and enhancing real-time decision-making. In the manufacturing realm, this translates to improved efficiency and reduced downtime. Instead of relying solely on centralized cloud servers, edge computing allows data processing to occur at the edge of the network, within the factory premises. This is particularly crucial in scenarios where immediate response is essential, such as predictive maintenance and quality control.
- 5G Connectivity
The advent of 5G technology is a game-changer for IIoT in manufacturing. The high-speed, low-latency capabilities of 5G networks enable seamless communication between devices and systems. This facilitates the transfer of large volumes of data in real time, fostering better collaboration and coordination in manufacturing processes. 5G also supports the proliferation of connected devices, paving the way for a more extensive and sophisticated IIoT ecosystem.
- Predictive Maintenance and Condition Monitoring
Predictive maintenance has gained significant traction in manufacturing, leveraging IIoT to monitor equipment conditions and predict potential failures before they occur. Through the use of sensors and data analytics, manufacturers can gather real-time information on machinery performance, enabling them to schedule maintenance activities proactively. This not only reduces downtime but also extends the lifespan of equipment, optimizing overall operational efficiency.
- AI and Machine Learning Integration
The integration of artificial intelligence (AI) and machine learning (ML) is a trend that continues to reshape IIoT in manufacturing. These technologies enable systems to learn from data patterns and make intelligent decisions autonomously. In the manufacturing context, AI and ML algorithms can analyze vast amounts of data to optimize production processes, improve product quality, and enhance supply chain management. From demand forecasting to quality control, AI-driven insights are becoming integral to informed decision-making.
- Digital Twins for Enhanced Simulation and Monitoring
Digital twins, virtual replicas of physical objects or systems, are becoming increasingly prevalent in manufacturing. This technology allows manufacturers to create a digital representation of their production processes, enabling comprehensive simulation and analysis. By combining real-time data from sensors with advanced modeling techniques, digital twins provide insights into performance, efficiency, and potential issues. This not only aids in refining processes but also supports predictive maintenance efforts, creating a more resilient and agile manufacturing environment.
- Cybersecurity Concerns and Solutions
As the connectivity and interdependence of IIoT systems grow, so does the concern for cybersecurity. Manufacturers are increasingly recognizing the importance of robust cybersecurity measures to safeguard sensitive data and ensure the integrity of their operations. Implementing end-to-end encryption, multi-factor authentication, and regular security audits are essential steps in mitigating the risks associated with IIoT. As the threat landscape evolves, manufacturers must remain vigilant in adopting and updating cybersecurity practices.
- Sustainability and Energy Efficiency
Sustainability has become a focal point in manufacturing, driven by environmental concerns and regulatory pressures. IIoT plays a pivotal role in achieving sustainability goals by optimizing energy consumption, reducing waste, and enhancing resource efficiency. Smart sensors and analytics help manufacturers monitor energy usage in real time, identify areas for improvement, and implement energy-saving measures. This not only aligns with environmental stewardship but also contributes to cost savings in the long run.
- Collaborative Robots (Cobots)
Collaborative robots, or cobots, are designed to work alongside human operators in manufacturing facilities. IIoT enables seamless collaboration between humans and cobots, fostering a more flexible and adaptive production environment. These robots can be equipped with sensors and connected to the IIoT ecosystem, allowing them to adapt to changing conditions and work collaboratively with their human counterparts. This trend enhances productivity and efficiency while addressing workforce challenges.
The trends in IIoT for manufacturing reflect a dynamic and ever-evolving landscape. From the integration of edge computing and 5G connectivity to the implementation of AI, machine learning, and digital twins, manufacturers are leveraging cutting-edge technologies to enhance efficiency, reduce downtime, and stay competitive in the global market. As the industry continues to embrace these trends, it is essential for manufacturers to prioritize cybersecurity, sustainability, and collaborative approaches to unlock the full potential of IIoT and usher in a new era of smart manufacturing.