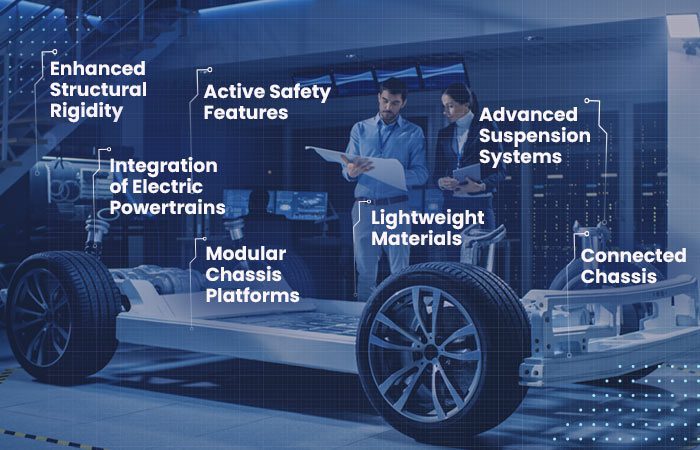
7 Biggest Trends in Automotive Chassis Design
As per a Boston Consulting Group report, the autonomous car market is predicted to hit $42billion by 2025, accelerating to $77billion by 2035. Primarily driven by a vision of an accident-free world, these smart, autonomous, and connected vehicles will give creative engineers and product planners extra design freedom, allowing them to explore new chassis concepts. Regardless, automotive chassis design has witnessed significant advancements in recent years as manufacturers strive to improve vehicle performance, handling, safety, and sustainability.
Here are some trends that are shaping the future of automotive chassis design:
- Lightweight Materials
With the increasing focus on fuel efficiency and reducing emissions, lightweight materials such as aluminum, carbon fiber, and high-strength steel are being utilized in chassis construction. These materials help in reducing overall vehicle weight while maintaining structural integrity.
For instance, aluminum alloy has higher energy absorption and low weight. Magnesium is another low-weight material that can be used for chassis design. It is 75% lighter than steel elements and 33% lighter than aluminum. Similarly, replacing traditional steel and cast iron components with polymer composites that directly reduce chassis and overall vehicle weight by up to 50%, thereby contributing to improved fuel efficiency.
- Integration of Electric Powertrains
The rise of electric vehicles (EVs) has led to the integration of electric powertrains within chassis design. Battery packs are often integrated into the floor of the vehicle, enabling a lower center of gravity, better weight distribution, and improved handling characteristics.
It is not just easier to design and assemble powertrain systems when they are combined into a single, compact mechanical enclosure. Integration also removes superfluous hardware and lessens the requirement for excess packaging materials, which greatly reduces the weight and volume of the system. Innovations that improve efficiency by boosting power density are also crucial. By running more efficiently and holding onto thermal energy, EVs that use technologies like automotive-qualified gallium nitride (GaN) technology can assist increase driving range. Reduced costs and fewer cooling components are the results..
- Modular Chassis Platforms
Modular architectures are gaining popularity as they allow for flexibility and cost savings across vehicle models. These platforms enable the sharing of components, including chassis structures, between different vehicle types, such as sedans, SUVs, and crossovers, maximizing economies of scale and reducing production costs.
When implemented properly, modularity is very advantageous to manufacturers, and electric vehicles are no exception. With only battery capacity and software separating base vehicles from more potent premium ones, there may be greater possibility for it because much of the technology can be common for a wider range of applications. OEMs are still experiencing a high learning curve with regard to EVs, and the market’s infancy is also adding rapidly varying elements to its requirements. OEMs may be able to respond more quickly to these quickly shifting client demands with a well-designed modular architecture.
- Advanced Suspension Systems
Manufacturers are incorporating advanced suspension technologies to enhance vehicle dynamics, ride comfort, and stability. Electronic suspension systems, adaptive dampers, and air suspension are becoming more common, providing improved handling through real-time adjustments to changing road conditions.
- Active Safety Features
Chassis design is evolving to accommodate various active safety features, including electronic stability control, forward collision warning, autonomous emergency braking, and lane departure warning systems. These features rely on sensor data and actuator systems integrated within the chassis to detect hazards and assist in mitigating potential accidents.
- Connected Chassis
The advent of connected vehicle technology has opened new possibilities for chassis design. Chassis systems can now communicate with other systems in the vehicle, enabling functions like predictive maintenance, remote diagnostics, and improved driver assistance features.
- Enhanced Structural Rigidity
Focusing on occupant safety, chassis designs are incorporating improved structural rigidity through advanced engineering techniques and materials. Reinforcements and reinforcements at key points, such as the A, B, and C-pillars and the roof, enhance crashworthiness and occupant protection.
Apart from these, automakers are also paying more attention to reducing noise, vibration, and harshness (NVH) levels inside the vehicle cabin. Chassis design is incorporating advanced damping materials, additional insulation, and strategic placement of components to reduce unwanted noise and vibrations. Plus, efficient aerodynamic designs are playing a crucial role in improving fuel efficiency and reducing drag. Chassis design is now being optimized to minimize airflow resistance, through features such as smooth underbody panels, active grille shutters, and streamlined body shapes.