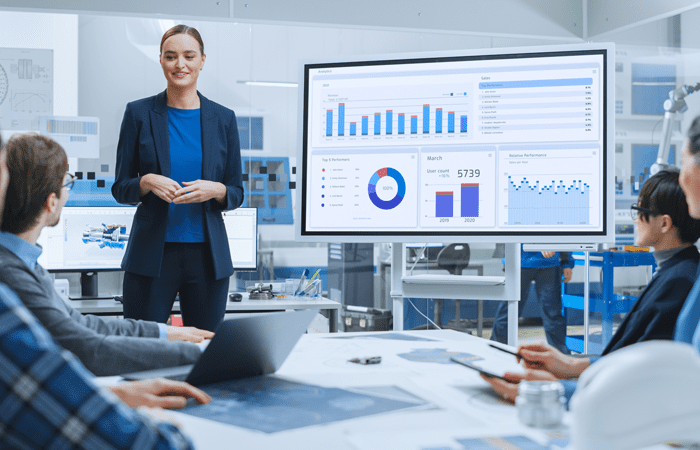
5 Plant Engineering Mistakes That Lead to Costly Turnarounds – And How to Avoid Them
Plant turnarounds are capital-intensive, high-risk projects that demand rigorous planning, cross-functional coordination, and precision execution. Whether the goal is to perform scheduled maintenance, upgrade systems, or ensure regulatory compliance, engineering plays a central role in determining the turnaround’s success. However, recurring engineering mistakes continue to lead to budget overruns, extended downtime, and compromised safety.
This blog outlines five critical engineering mistakes that commonly result in costly turnarounds across industrial facilities—and provides practical guidance on how to mitigate them.
- Inadequate Front-End Engineering and Planning (FEEP)
What Goes Wrong:
A significant number of turnarounds fail to meet performance targets due to insufficient definition in the early phases. Poor or incomplete FEED (Front-End Engineering Design) undermines downstream activities, resulting in rework, misaligned procurement, and scope changes mid-execution.
Impacts:
- Scope creep
- Poor contractor performance
- Inaccurate budgeting and scheduling
- Inefficient material procurement
Mitigation Strategy:
- Implement a stage-gated FEEP process that includes feasibility analysis, site surveys, asset condition assessments, and constructability reviews.
- Involve operations, reliability, and safety teams early.
- Use 3D modeling and digital twins to validate designs before execution.
- Conduct formal HAZOP (Hazard and Operability) studies.
According to a McKinsey report, 30–40% of cost overruns in large industrial projects stem from inadequate front-end planning.
- Overreliance on Legacy Asset Data
What Goes Wrong:
Many engineering teams rely on outdated or incomplete documentation from previous turnarounds. Without accurate P&IDs, instrumentation layouts, and mechanical drawings, teams make assumptions that introduce risk.
Impacts:
- Equipment mismatch
- Design clashes during construction
- Late-stage design changes
- Safety non-compliance
Mitigation Strategy:
- Digitize and validate existing plant documentation prior to the turnaround.
- Use laser scanning, drones, or photogrammetry for as-built modeling.
- Establish a single source of truth (SSOT) through a centralized engineering data platform.
Studies show that 40% of field rework is due to inaccurate or missing documentation.
- Engineering-Procurement Misalignment
What Goes Wrong:
In many turnarounds, procurement is not fully aligned with engineering deliverables. Long-lead items may not be identified in time, and BOMs (Bill of Materials) are finalized too late for strategic sourcing.
Impacts:
- Equipment delays
- Increased costs due to expedited shipping
- Supplier quality issues
- Rescheduling of critical-path activities
Mitigation Strategy:
- Use 4D/5D planning tools to integrate engineering deliverables with procurement timelines.
- Lock long-lead items during early engineering phases.
- Engage vendors during FEED for accurate specification matching.
- Conduct procurement readiness reviews prior to mobilization.
A study by ARC Advisory Group noted that 25–30% of turnaround delays are due to material availability issues.
- Incomplete Risk and Constructability Reviews
What Goes Wrong:
Risk assessments often focus only on safety hazards, neglecting constructability issues such as limited space, crane access, weather delays, or commissioning complexities. Engineering drawings may look feasible on paper but prove impractical in real plant conditions.
Impacts:
- Last-minute design modifications
- Interdisciplinary clashes
- Extended outage periods
- Cost escalations due to unplanned labor or equipment rental
Mitigation Strategy:
- Incorporate constructability and maintainability reviews into the design process.
- Simulate construction and commissioning sequences using BIM (Building Information Modeling) and 4D planning.
- Involve field engineers and contractors during detailed design.
- Create contingency buffers based on risk modeling.
According to Independent Project Analysis (IPA), constructability issues contribute to 10–15% of schedule overruns in capital projects.
- No Feedback Loop from Previous Turnarounds
What Goes Wrong:
Engineering teams often start from scratch without leveraging insights from previous turnaround cycles. Critical lessons—such as what failed, what worked, and what could have been improved—are not systematically captured.
Impacts:
- Repetition of past mistakes
- Lack of historical benchmarking
- Missed optimization opportunities
- Cultural inertia against continuous improvement
Mitigation Strategy:
- Conduct formal post-turnaround reviews and capture engineering-specific data points.
- Maintain a structured lessons-learned database.
- Create key performance indicators (KPIs) to track engineering accuracy, change orders, and field deviations.
- Integrate lessons learned into future FEED packages and project management workflows.
How TAAL Tech Helps You Engineer Smarter Turnarounds
Avoiding these engineering pitfalls requires not only strong domain expertise but also a multi-disciplinary, system-driven approach. TAAL Tech is a proven system integrator and engineering solutions provider that partners with plant operators to deliver cost-effective, risk-mitigated, and time-bound turnaround engineering services.
TAAL Tech’s Capabilities Include:
- FEED and Detailed Engineering:
Comprehensive scope definition with PFDs, P&IDs, GA drawings, and 3D models for optimized execution.
- Digital Twin Integration:
Advanced plant modeling and simulation for clash detection, constructability analysis, and real-time planning.
- Procurement Support:
Vendor engagement, material take-off, long-lead item tracking, and procurement alignment with project milestones.
- Cross-Disciplinary Engineering Teams:
Mechanical, civil/structural, E&I, and process engineers working in concert with planners and project controllers.
- Post-Turnaround Analysis:
Structured documentation of lessons learned, asset condition monitoring, and O&M insights for continuous improvement.
With delivery centers and engineering teams experienced in global plant standards, TAAL Tech ensures precision, collaboration, and innovation at every phase of your turnaround lifecycle.
Engineering mistakes are one of the most controllable factors affecting turnaround costs and timelines. By improving scope clarity, integrating procurement early, validating documentation, and fostering knowledge transfer, plant operators can significantly enhance turnaround performance.
Partnering with an experienced system integrator like TAAL Tech not only de-risks the process but helps you transition to a more data-driven, proactive model of shutdown and turnaround execution.