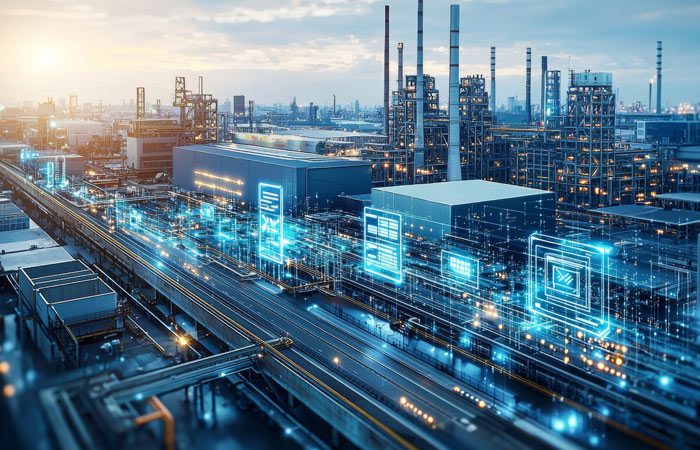
How to Optimize Your Existing Plant Infrastructure in Europe?
As Europe accelerates its sustainability agenda under the European Green Deal and Fit for 55 package, industrial players face a transformative challenge: how to decarbonize operations without compromising productivity or profitability. With climate targets tightening and stakeholder expectations evolving, optimizing existing plant infrastructure has become a strategic imperative—not just an environmental responsibility.
Engineering for sustainability isn’t just about building new greenfield projects. It’s increasingly about reimagining, retrofitting, and reengineering what already exists.
This article explores how industrial plants across Europe can lead this transformation through a mix of digital innovation, operational optimization, and strategic engineering.
Why Optimizing Existing Infrastructure Matters?
Europe is home to some of the world’s most mature industrial assets, especially in sectors like chemicals, oil and gas, pharmaceuticals, power generation, and manufacturing. Much of this infrastructure was developed decades ago, with minimal regard for today’s carbon benchmarks or circular economy models. Replacing entire plants is rarely feasible due to cost, regulatory complexities, and downtime.
Instead, the focus must be on sustainable retrofitting and smart optimization—an approach that reduces emissions, energy consumption, and waste while enhancing system efficiency and asset life.
As per McKinsey, up to 40% of emissions reductions in industry could come from optimizing existing operations, including upgrades to energy systems, predictive maintenance, and digital process controls.
- Digital Twins & Predictive Analytics: Seeing the Invisible
Digitalization is the cornerstone of modern sustainable engineering. By creating digital twins—virtual replicas of physical assets—plant operators can simulate, analyze, and predict how systems behave under different loads, conditions, and process changes.
In the European context, several projects under the Horizon Europe programme are actively funding the development of AI-powered twins for industrial applications.
For instance, the DESTINY project aims to optimize thermal processes in ceramic and cement plants using real-time data and simulations, potentially reducing energy demand by up to 20%.
Key benefits include:
- Real-time monitoring of energy consumption.
- Early identification of inefficiencies or leaks.
- Optimization of asset performance with minimal intervention.
By combining digital twins with predictive maintenance, facilities can avoid energy-intensive equipment failures, reduce unplanned downtime, and extend equipment life.
- Energy Optimization Through Process Reengineering
Energy efficiency remains the quickest route to both emission reduction and cost savings. Engineering teams can redesign core plant processes to reduce energy intensity per unit of output.
Strategies include:
- Heat recovery systems: Retrofits such as regenerative heat exchangers or heat pumps can recover and reuse waste heat. In Germany, several industrial clusters have adopted this, particularly in food and beverage plants.
- Process electrification: Replacing fossil-fuel-based systems (like steam boilers) with electric alternatives powered by renewable sources. Norway’s heavy industry has made notable progress here, driven by its hydropower grid.
- Variable frequency drives (VFDs) on motors and pumps to reduce energy wastage.
- Compressed air systems optimization, which is often overlooked but can account for 10–15% of a plant’s total energy use.
According to the International Energy Agency (IEA), these types of retrofits can reduce energy use in EU plants by up to 25% when combined strategically.
- Retrofitting for Renewable Integration
Many older facilities were not designed to accommodate renewables. However, retrofitting for solar panels, wind turbines, or integrating Power Purchase Agreements (PPAs) can provide a clean source of energy and reduce grid dependency.
One notable example is BASF’s Ludwigshafen site in Germany, which is undergoing extensive redesign to incorporate on-site solar and hydrogen-based systems. The aim is to decarbonize one of Europe’s largest chemical plants while maintaining output.
Key retrofit solutions:
- Roof-top or on-site solar PV installations.
- Battery energy storage systems (BESS) for peak load shaving.
- Smart grid integration using microgrid controllers.
- Heat storage solutions in thermal-intensive plants.
- Water and Waste Optimization: Circular Engineering
The EU’s Circular Economy Action Plan pushes industries to minimize waste and resource use. Water usage, in particular, is critical as drought risk increases in Southern and Central Europe.
Plant optimization tactics include:
- Water recirculation systems and zero-liquid discharge technologies.
- Retrofitting for greywater reuse and rainwater harvesting.
- Waste heat-to-water desalination in coastal areas.
- Closed-loop manufacturing models that reuse waste as input.
For example, a Nestlé plant in Spain has reduced water consumption by 60% since 2010 through smart water reuse systems and process redesign.
On the solid waste side, material recovery facilities (MRFs) can be integrated into existing plants to sort, recycle, and reintroduce valuable raw materials into the production cycle.
- Emission Monitoring and Compliance Upgrades
With the EU Emissions Trading System (ETS) expanding to include more sectors, plants must ensure compliance while maintaining operational continuity. Retrofitting with advanced emissions monitoring systems allows for real-time compliance tracking and emissions benchmarking.
Some engineering-driven measures include:
- Upgrading stack monitoring with continuous emissions monitoring systems (CEMS).
- Installing selective catalytic reduction (SCR) for NOx reduction.
- Retrofitting scrubbers for sulfur and particulate control.
France’s TotalEnergies has implemented an AI-enhanced emissions monitoring system across multiple refineries, significantly improving reporting accuracy and identifying early anomalies.
- Workforce Enablement Through Engineering Innovation
Even the best-engineered upgrades fail without empowered personnel. A sustainable plant is not just about hardware—it’s about people and processes. Engineering teams must work closely with operations and maintenance staff to ensure new systems are well-integrated and continuously optimized.
Strategies to consider:
- Digital upskilling programs for plant staff in data analytics and IoT systems.
- Collaborative decision-making tools (like dashboards or mobile platforms).
- Remote monitoring and AR-based maintenance tools to reduce travel and downtime.
This human-machine synergy creates a responsive, resilient operational environment capable of adapting to new sustainability requirements.
- Financing & Incentives: Making the Business Case
Sustainability retrofits require upfront investment, but the long-term ROI can be significant. Engineering teams must work closely with finance and ESG departments to build compelling business cases.
Options in Europe include:
- EU Innovation Fund: For large-scale decarbonization projects.
- National energy efficiency grants (like Germany’s BEG program or France’s ADEME initiatives).
- Green bonds and ESG loans tied to performance benchmarks.
- Carbon credits for verifiable emissions reductions.
A study by the European Investment Bank (EIB) shows that industrial energy retrofits typically yield a payback within 3–7 years, especially when layered with incentives.
How TAAL Tech Can Support Your Sustainability Journey
At TAAL Tech, we specialize in helping industrial clients across Europe optimize their existing plant infrastructure with a focus on sustainability, efficiency, and future readiness. Our engineering teams offer deep domain expertise in mechanical, electrical, process, and digital engineering—allowing us to deliver tailored retrofitting strategies, energy audits, and digital twin implementations.
Whether it’s upgrading legacy systems for improved energy performance, integrating renewable energy solutions, or deploying predictive maintenance platforms, TAAL Tech delivers end-to-end support from feasibility to implementation. Our experience across diverse sectors—such as oil & gas, chemicals, utilities, and manufacturing—makes us a trusted partner in aligning operational goals with Europe’s decarbonization mandates.
Engineering the Future, Sustainably
Sustainable transformation is no longer a choice for Europe’s industrial sector—it’s an obligation. But it doesn’t always require radical overhauls. Thoughtful engineering can unlock tremendous value from existing assets.
By integrating digital tools, upgrading core processes, enhancing energy and resource efficiency, and empowering teams, companies can align operational excellence with climate leadership. Europe’s industrial leaders must now pivot from viewing sustainability as a constraint to recognizing it as a catalyst for innovation, efficiency, and competitiveness.