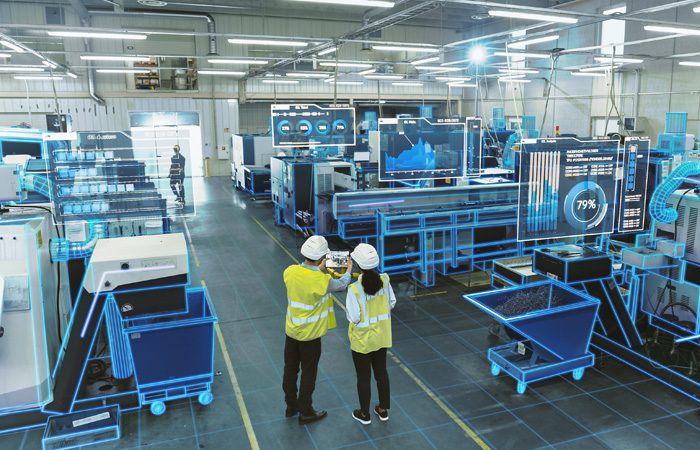
How Digital Twins Are Transforming Maintenance, Simulation, and Predictive Performance in Plants
Walk into any modern industrial plant today, and you’ll likely see a mix of decades-old machines and cutting-edge automation systems. Bridging the gap between these worlds—and making everything work smarter—is a powerful concept called the digital twin.
More than just a buzzword, digital twins are fast becoming essential to how plants are operated, maintained, and improved. They offer a virtual replica of a real system, letting engineers monitor performance, run simulations, and even predict future outcomes—all without touching a single piece of hardware.
Here’s how digital twins are quietly revolutionizing plant operations from the inside out.
Maintenance That Sees Problems Before You Do
If you’ve ever had a critical machine go down without warning, you know how disruptive and expensive unplanned downtime can be. Traditional maintenance models—waiting for something to break or servicing on a fixed schedule—just don’t cut it anymore.
This is where digital twins really shine. By constantly collecting data from sensors and control systems, they help detect early warning signs that something isn’t right. Is a pump vibrating more than usual? Is a motor running a bit hotter than expected? A digital twin picks that up and flags it before failure hits.
The result? Predictive maintenance that’s proactive instead of reactive. Instead of rushing to fix what’s broken, teams can plan interventions when they’re needed most—minimizing downtime and avoiding over-servicing.
Simulation Without the Risk
In the physical world, trial and error is expensive. Testing a new configuration or process means taking equipment offline, burning resources, and hoping it works. But in the digital twin world? You can model it, tweak it, and test it—all without disrupting real operations.
Imagine being able to simulate:
- What happens if you ramp up production by 15%?
- How a new energy-saving measure would affect throughput?
- Whether a new layout could cut down on transport time across the plant?
With a digital twin, these “what if” questions become part of everyday decision-making. You’re not guessing—you’re seeing the outcomes in a virtual model that mirrors the real world.
This makes digital twins an incredible tool not just for operations, but also for continuous improvement, design validation, and change management.
Predicting What’s Next (and Preparing for It)
Plant managers and engineers don’t just care about what’s happening now—they need to know what’s coming next. That’s where the predictive power of digital twins really takes things up a notch.
By analyzing trends in data over time and running simulations forward, digital twins can forecast:
- When performance will start to dip
- When energy usage is likely to spike
- How equipment will behave under different future loads
Think of it as your plant’s crystal ball, built on real data.
This foresight helps companies budget better, manage risk, and avoid surprises. Whether it’s planning an upgrade, managing lifecycle costs, or preparing for seasonal demand changes, predictive insights give decision-makers a serious edge.
More Than Performance: Supporting Sustainability and Compliance
Efficiency is great—but what about sustainability? With environmental goals and regulations becoming more stringent, plants also need to optimize their carbon footprint, water use, and emissions.
Digital twins help here too.
They can simulate energy usage, monitor environmental KPIs, and suggest greener configurations—all without trial and error. They also provide a digital record of how systems are operating over time, which is useful for audits, reporting, and regulatory compliance.
So in addition to making operations smarter, digital twins also support more sustainable and accountable practices.
Turning Potential into Practice
Of course, getting value from digital twins isn’t just about installing software—it takes the right expertise to build accurate models, integrate systems, and interpret the data. That’s why many organizations turn to engineering service partners to guide them through the process.
TAAL Tech, for example, supports manufacturers and plant operators in deploying digital twin solutions that align with their operational goals. From sensor mapping and real-time data integration to performance modeling and predictive analytics, TAAL Tech helps clients unlock the full value of digital twin technology in the context of their plant systems.
The Future Is Digital—and It’s Already Here
Digital twins aren’t futuristic concepts anymore—they’re quietly reshaping how modern plants run, improve, and evolve. Whether it’s preventing downtime, testing smarter strategies, or forecasting what’s next, these virtual replicas are delivering real-world impact.
As more organizations embrace this technology, one thing becomes clear: the plants that thrive tomorrow will be the ones that start building their digital twin foundation today.