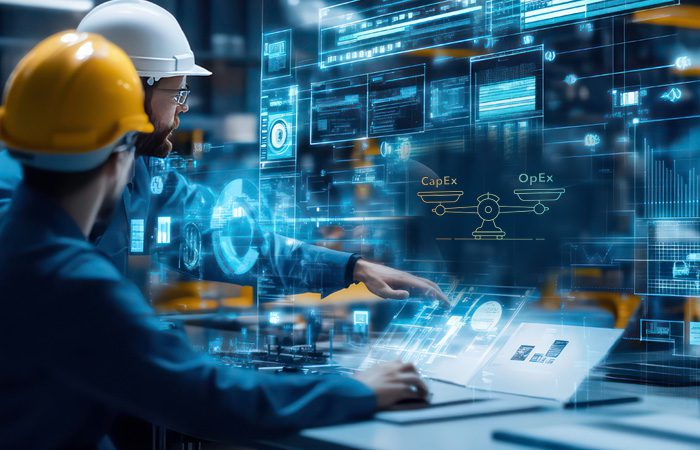
Engineering with ROI in Mind: How to Balance CapEx and OpEx in Plant Projects in Europe
There’s a quiet shift happening across plant floors and boardrooms in Europe. You can see it in the way procurement teams negotiate, in how design engineers are being looped into operational strategy conversations, and in how sustainability isn’t just a CSR checkbox anymore — it’s a cost center and a value driver all at once.
At the heart of this shift is a single, deceptively simple question:
“What’s the return on engineering?”
Not just return on investment. Not just whether the budget was followed or the commissioning was on time. But whether the engineering decisions made at the outset — the materials chosen, the control systems integrated, the HVAC layouts finalized — have been made with ROI in mind, across both CapEx and OpEx.
Because in Europe today, where regulations are tightening, energy prices remain volatile, and ESG pressure is real, balancing CapEx and OpEx is no longer a financial optimization exercise. It’s engineering strategy.
And frankly, many are still getting it wrong.
The Old Way vs. The Smarter Way
Traditionally, CapEx (capital expenditure) was about the here and now: What’s the lowest cost to build this facility or line and get it operational? OpEx (operational expenditure), on the other hand, was future-you’s problem. Energy bills, maintenance routines, downtime — let the ops team handle it.
But this “handoff” mentality no longer works. Let’s take a simple example:
You save €150,000 upfront by choosing a non-inverter HVAC system. But that decision locks you into 10 years of high energy consumption and reactive maintenance. Over the lifecycle, that €150k saving is dwarfed by the €1.2 million you’ll spend operating it.
So what’s smarter? Spending a little more now — and designing for efficiency, maintainability, and flexibility — to save significantly more in the long run.
This is where leading European manufacturers are flipping the script.
ROI-Led Engineering: What It Looks Like in Practice
Let’s break this into three ideas that are driving ROI-first engineering decisions across Europe:
- Design for Total Cost of Ownership, Not Lowest CapEx
You wouldn’t buy a cheap car that guzzles fuel and breaks down every month — so why build a facility that behaves that way?
Smart engineering teams are now evaluating every equipment or design choice through the lens of TCO — Total Cost of Ownership. This includes:
- Energy consumption over 10–15 years
- Spare parts and maintenance schedules
- Expected downtime
- End-of-life and recyclability
For example, in a pharmaceutical plant retrofit in Belgium, one client opted for slightly higher-spec pumps with embedded diagnostics. Over three years, they reduced unplanned downtime by 40%, easily surpassing their ROI target — and avoiding multiple product batch losses.
- Factor Flexibility into the Initial Engineering
Markets shift. Demand forecasts change. And product lifecycles are shrinking. Which means the plants we design today must be modular, reconfigurable, and digitally intelligent.
An engineering choice that looks like a minor expense — say, running extra conduits for future lines or integrating scalable PLCs — can save months and millions later when you need to scale or pivot production.
European food and beverage companies are already embracing this. In one project in Denmark, a beverage client engineered “over-capacity” into utility systems — anticipating expansion within 3 years. When the expansion came? No downtime, no redesign, no headaches. Just plug and play.
- Use Digital Simulations and Energy Modeling Early
Most engineering budgets treat energy modeling and digital twin simulations as “nice to have.” But leading-edge projects are proving these tools are among the best ROI enablers.
With energy prices in Europe fluctuating and regulations like the Energy Efficiency Directive pushing hard limits, simulating your facility’s performance before construction starts is a game-changer.
Using early-stage BIM, CFD simulations, and dynamic energy models, engineering teams can optimize:
- Airflow for HVAC efficiency
- Process layouts for reduced pumping power
- Lighting design for daylight utilization
- Renewable energy integration
A manufacturing plant in Italy used simulation to re-orient their rooftop solar layout and optimize natural ventilation. Estimated payback: 2.8 years. Without the model? They would have designed it wrong — and locked in 15 years of underperformance.
What’s Driving This Shift in Europe?
Europe is uniquely positioned to lead ROI-first engineering because of three pressures converging:
- Regulations with Teeth:
From CSRD reporting to the EED, European plants now need to show efficiency, not just claim it. - Sustainability Pressure:
Investors, customers, and governments are asking tougher questions. ESG isn’t optional — it’s tied to credit ratings and procurement eligibility. - Energy Volatility:
The aftermath of energy shocks post-Ukraine crisis has made OpEx — especially utility bills — too big to ignore. Engineering teams now face real-time cost scrutiny.
So, Where Do You Begin?
If you’re an OEM, EPC, or plant owner reading this, the roadmap doesn’t have to be complex. But it does require intentionality. Here’s how to start balancing CapEx and OpEx with ROI at the core:
- Involve operations early in the design phase — not after commissioning.
- Insist on lifecycle costing in your procurement RFPs.
- Don’t cut digital tools from pre-construction modeling budgets — they’re your visibility and control levers.
- Audit your previous projects to identify where CapEx-centric decisions led to costly OpEx.
- Work with engineering partners who understand both the technical and financial impacts of their choices.
How TAAL Tech Engineers for ROI
At TAAL Tech, we believe engineering isn’t just about blueprints — it’s about business outcomes. In our work across process plants, manufacturing units, and retrofit projects in Europe, we prioritize ROI at every stage:
- Our multidisciplinary teams combine design engineers, energy modelers, and operations specialists to optimize both CapEx and OpEx.
- We use advanced simulations, digital twins, and lifecycle costing tools from the earliest stages.
- With our hybrid delivery model, we bring cost-effective design support without compromising European standards or compliance.
Whether it’s reducing energy loads in a HVAC redesign, enabling predictive maintenance through smart instrumentation, or supporting greenfield plant planning — we engineer with your long-term ROI in mind.
Final Word: Engineering is a Financial Decision
Engineering may live on the technical side of the business, but its consequences are felt on the balance sheet.
In Europe’s evolving industrial environment, the smartest plant isn’t just the most automated or the most modern. It’s the one whose engineering decisions are aligned to profitability, adaptability, and sustainability — from day one.
So, the next time you’re faced with a plant design or upgrade decision, ask not just “How much does it cost?”
Ask: “How well will it perform over time — and how smart was this investment?”
Because that’s what ROI-first engineering looks like.